Revolutionizing Industrial Efficiency: A Comprehensive Exploration of Dry Bulk Storage Silos
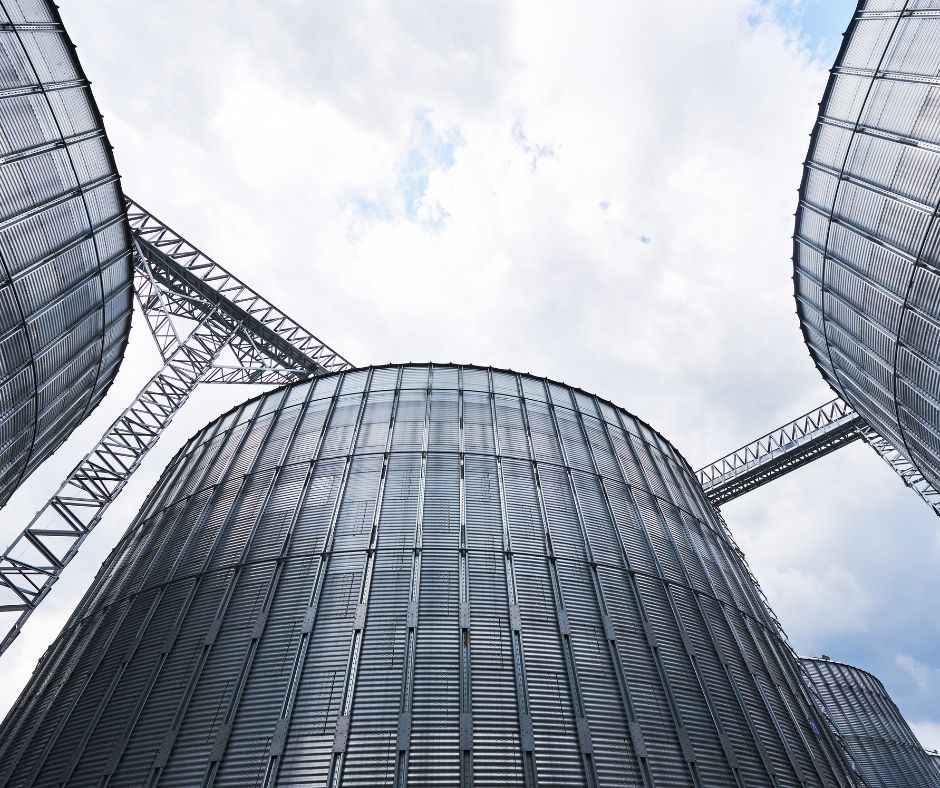
In the expansive world of industrial storage solutions, Dry Bulk Storage Silos emerge as transformative structures, reshaping the landscape of how bulk materials are managed across a myriad of sectors. From the fields of agriculture to the intricacies of manufacturing, these specialized silos play a central role in ensuring seamless operations and optimizing workflow. This thorough exploration aims to delve deeply into the multifaceted aspects of Dry Bulk Storage Silos, spanning their diverse types, design considerations, applications across industries, technological advancements, and their significant contributions to sustainable practices.
Types of Dry Bulk Storage Silos
Dry Bulk Storage Silos are not a one-size-fits-all solution; instead, they manifest in various configurations to meet the specific demands of different industries. Each type brings forth unique advantages tailored to specific materials and storage requirements:
-
Flat-Bottom Silos: Suited for the storage of grains and seeds, providing stability and efficient space utilization while maintaining easy access for retrieval.
-
Cone-Bottom Silos: Designed for free-flowing materials, these silos ensure complete discharge, minimizing material residues and promoting efficient material handling.
-
Hopper-Bottom Silos: Ideal for materials with varying particle sizes, facilitating controlled flow and preventing material bridging.
-
Multi-Compartment Silos: Tailored for industries requiring segregated storage, these silos enhance organization and retrieval efficiency, accommodating different materials within a single structure.
Design Considerations for Optimal Efficiency
Efficiency in Dry Bulk Storage Silos is contingent on thoughtful design considerations. This section delves into the critical elements that contribute to the seamless functionality of these structures:
-
Material Flow Patterns: Understanding and optimizing material flow patterns to prevent clogs and ensure a continuous and smooth discharge process.
-
Wall Friction: Mitigating wall friction to enhance material flow and prevent the accumulation of material on the silo walls, thereby facilitating consistent flow.
-
Aeration Systems: Incorporating aeration systems to maintain material quality by preventing degradation and ensuring uniform conditions throughout the stored mass.
-
Safety Features: Integrating safety measures to create a secure storage environment, safeguarding both the stored materials and the personnel involved in operational processes.
Applications Across Industries
The versatility of Dry Bulk Storage Silos is evident in their widespread applications across diverse industries, each benefiting from their specialized features:
-
Agriculture: Serving as storage units for grains, seeds, and fertilizers, Dry Bulk Storage Silos contribute to efficient farm management, ensuring a continuous and reliable supply chain for crop production.
-
Manufacturing: Housing raw materials such as powders, granules, and other bulk materials, these silos facilitate streamlined production processes, minimizing downtime and optimizing manufacturing efficiency.
-
Construction: Storing bulk materials like cement, aggregates, and other construction materials, Dry Bulk Storage Silos ensure a constant supply for construction projects, contributing to project timelines and resource management.
-
Food and Beverage: Safeguarding both raw ingredients and processed products, these silos uphold stringent quality standards, preserving the integrity of the food supply chain.
Advancements in Silo Technology
The evolution of Dry Bulk Storage Silos has been significantly influenced by technological advancements, ushering in an era of smart and automated storage solutions:
-
Smart Monitoring Systems: Real-time monitoring of material levels using Internet of Things (IoT) technologies, enabling proactive management, timely replenishment, and preventing stockouts.
-
Automated Material Handling: Integration of automated systems for loading and unloading, reducing manual labor, and enhancing operational efficiency through precision and speed.
-
Predictive Maintenance: Utilizing predictive analytics to anticipate maintenance needs, minimizing downtime, and optimizing the overall lifespan of Dry Bulk Storage Silos.
Sustainable Practices in Bulk Material Storage
In an era where sustainability is paramount, Dry Bulk Storage Silos contribute significantly to environmentally friendly practices:
-
Energy-Efficient Designs: Incorporating features that reduce overall operational costs and energy consumption, aligning with the broader industry shift towards sustainable and cost-effective solutions.
-
Material Recycling: Facilitating the recycling and repurposing of materials stored in silos, contributing to circular economy principles by minimizing waste and promoting resource efficiency.
-
Reduced Footprint Solutions: Compact silo designs that optimize space utilization, minimizing the environmental footprint of industrial storage facilities while maximizing storage capacity.
Conclusion:
Dry Bulk Storage Silos stand as stalwart pillars in the realm of industrial storage, influencing efficiency, sustainability, and operational success. From their diverse applications to nuanced design considerations and recent technological advancements, these silos represent the epitome of modern Storage tanks solutions. As industries continue to evolve towards streamlined and sustainable practices, the role of Dry Bulk Storage Silos remains pivotal, shaping a future where optimal material management becomes synonymous with industrial progress and responsible resource utilization.